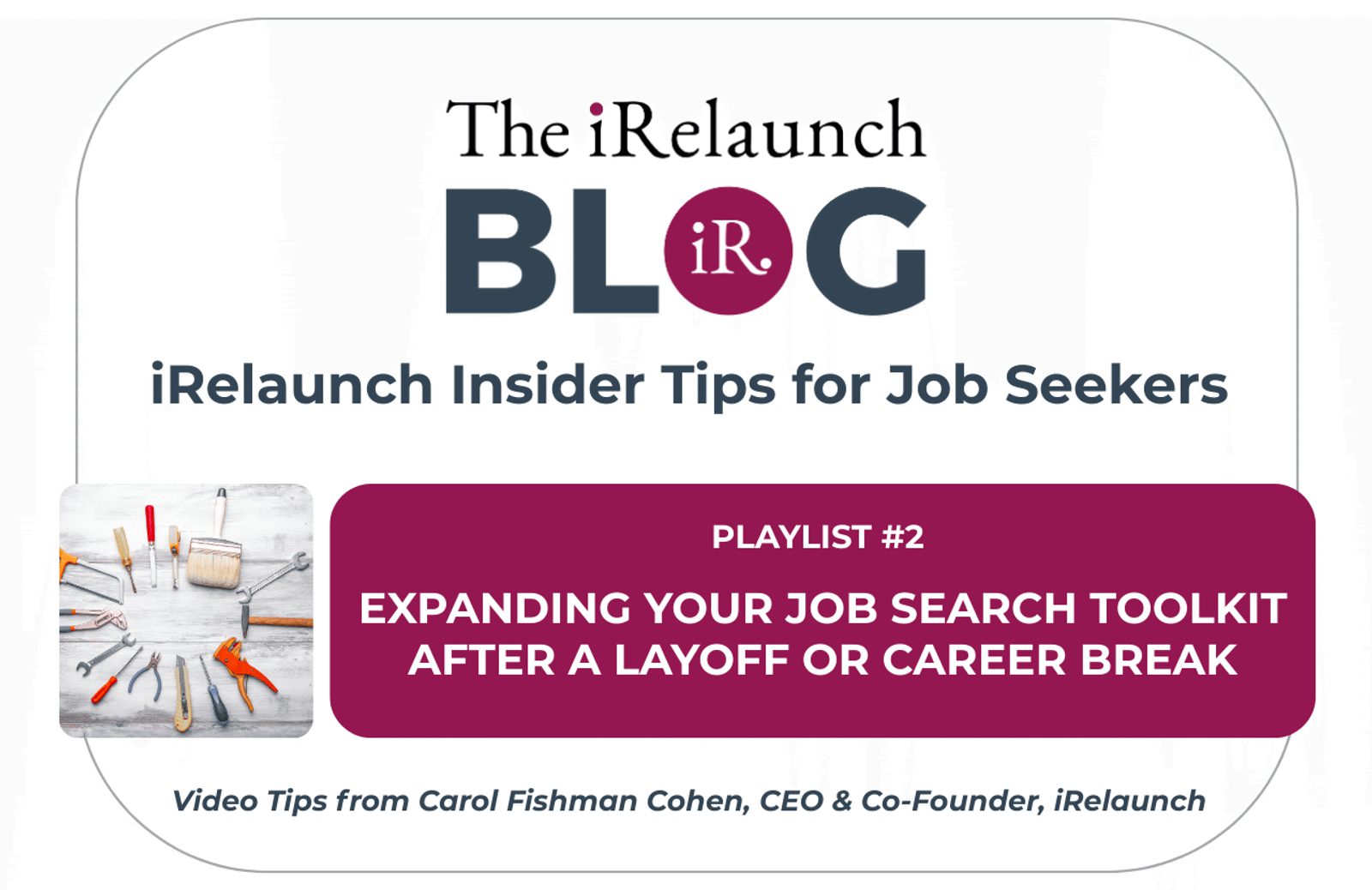
I have a degree in Mechanical Engineering and an MBA. I spent 16 years in quality engineering management before taking an 11-year career break. After looking at current job postings in my field, I felt my skills were really outdated and knew I would need a thorough education in LEAN Manufacturing techniques in order to be hired.
I took an online class in Six Sigma and an eight-day course in LEAN Manufacturing held at a manufacturing firm. This was a course engineers are sent to by their companies. So it was expensive. It was one day a week for eight weeks. We did some simple projects in that factory. At the LEAN course, I made a big impression. I was the only one with time to do homework! I asked the director of manufacturing, a fellow attendee, if I could do a few projects for him, for the experience. I did a LEAN value stream map with time studies for incoming inspection. I presented this to the managers and planners, walking them through the exercise of identifying waste. Most importantly, I had an actual lean project I could speak about in interviews.
Additionally, I went on every plant tour I could, via the Greater Boston Manufacturing Partnership. I went to meetings of three professional organizations - the Society of Women Engineers, the American Society for Quality, and the American Society of Mechanical Engineers. I attended the Northeast Shingo Conference that focuses on the latest developments in lean practices. Finally, I read LEAN blogs and about 10 books. The whole process took about nine months.
I found I was really able to carry my side of a conversation with all this exposure - so it wasn't my experiences I was talking about, but something new I had seen or heard about.
Lastly, I called an outplacement firm a neighbor had used during a layoff. I asked him if he ever worked with individuals. We met four times. He rewrote my resume, found value where I hadn't, and gave me strategies and tactics for dealing with salary discussions.
After three interviews, I was hired as a Business Process Improvement Specialist at MKS Instruments in Andover in a temporary position. I had been watching this company, since someone I hired 15 years ago and with whom I had worked prior to that, works in management there! Then I sat next to their new VP of Quality at an ASQ professional association meeting. So I sent the VP my resume and I got an interview."
Note: Six months later they bumped up Loraine's pay and made her a permanent employee, and two months after that, Loraine was promoted to Senior Quality Engineer.
Did this story motivate you or inspire you!?
Do you have a relauncher success story of your own to share with us and the rest of the relauncher community?
Sharing your inevitable success is a great way to give back as your story will inspire and motivate other relaunchers, especially if your story is not the typical story that is told.
It is our hope that all relaunchers are able to see themselves reflected in relauncher success stories as we all know how important representation is. We respectfully ask you to share only the details of your relaunch you are comfortable sharing, but to indeed share your story with us so we can be sure to document and feature a more diverse population of relauncher experiences, background and identities.